DMG 5-Achs-Fraesen und Drehen kombinierte Bearbeitung ultraduenner Gehaeuse
Schlüsselwörter: Fräs- und Verbundbearbeitung Drehen, ultra-dünnes Gehäuse Bearbeitung, Fräsen und Drehen von Verbundbearbeitungswerkzeugen, Fräs- und Bearbeitungshalterung Fahrzeugverbundbauweise
Die Auswahl der Fräs- und Dreh Composite-Verarbeitung Ausrüstung
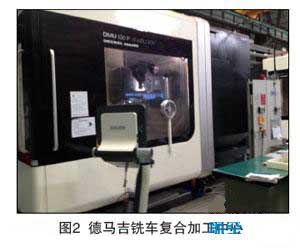
Die ultradünne Schalenbearbeitungsanlage wird aus dem 5-Koordinaten-Fräs- und Drehbearbeitungszentrum von Demag ausgewählt (siehe Abbildung 2). Die Maschine verwendet einen elektrischen Spindelkopf mit einem Winkel von 45 ° und wird von einem Linearmotor angetrieben. Das Servoantriebssystem zeichnet sich durch hohe Präzision, gute Zuverlässigkeit und schnelle Reaktion aus. Es gibt genügend statische und dynamische Steifigkeit, um sicherzustellen, dass das System eine gute dynamische Qualität und thermische Stabilität aufweist. Das Gerät sollte über eine hohe Präzision, hohe Zuverlässigkeit und eine Ethernet-Schnittstelle verfügen, um mit Computern und anderen Geräten zu vernetzen. Es realisiert die Übertragung von CNC-Bearbeitungsprogrammen, verschiedenen Prozessparametern und Maschinenzustandsinformationen und kann sich an die Bearbeitung schwer zerspanbarer Werkstoffe wie Hochtemperaturlegierungen und Titanlegierungen anpassen. Es kann Fräsen, Drehen, Bohren, Spreizen, Reiben, Bohren usw. in einer Aufspannung ausführen und kann zum präzisen Positionieren von Löchern in Luft- und Raumfahrtteilen sowie zum Vorschlichten und Schlichten von Außenflächen verwendet werden. Die Maschine ist kraftvoll gefräst und mit der Frässoftware SHOPMILL ausgestattet. Die Werkbank kann ein dynamisches Gleichgewicht herstellen und den Auswuchtpunkt analysieren, um die Drehfunktion zu unterstützen. Mit der Online-Erkennungsfunktion kann eine Online-Simulation von Auto und Fräsen realisiert werden. Die wichtigsten technischen Parameter der Maschine sind wie folgt:
Achsen-Verfahrweg: ≥1250mm;
Y-Achsen-Reisen: ≥1000mm;
Verfahrweg Z-Achse: ≥1000mm;
Werkbank größe: ≥ φ1250mm;
Maximaler Drehdurchmesser: ≥ φ1400mm;
Belastung der Werkbank: ≥2000 kg.
Drehbereich der C-Achse (Werkbank): ≥ ± 360 °, Positioniergenauigkeit: ≤ 7 ′ ′, Wiederholungspositioniergenauigkeit: ≤ 4 ′ ′.
Arbeitstisch fräsen maximale geschwindigkeit: ≥20r / min,
Maximale drehgeschwindigkeit: ≥500r / min,
Maximales Drehmoment (S1): ≥ 5400 N • m,
Maximale Leistung zum Wenden (S1): ≥35 kW.
2. Vorrichtungsdesign für den Fräsprozess
Die kombinierte Bearbeitungstechnologie Fräsen und Drehen muss die Bearbeitung der meisten Dimensionen in einer Aufspannung realisieren, und die Werkzeugaufnahme ist entscheidend für das Spiel. Andernfalls muss es viele Male gespannt werden, was die Verarbeitungseffizienz zwangsläufig verringert. Die Technologie des Fräsens und Drehens der Verbundbearbeitungstechnik besteht darin, dass die Innenfläche im Allgemeinen durch Drehen gedreht wird, die Außenfläche Drehen und Bohren und Fräsen umfasst und die Endfläche oder das radiale Loch durch Bohren, Bohren und Reiben bearbeitet wird. Daher muss für die kombinierte Bearbeitung von Fräsen und Drehen eine Vorrichtung entwickelt werden, die innen und außen positioniert und eingespannt werden kann und schnell zerlegt werden kann. Die ultradünne kombinierte Bearbeitungsvorrichtung zum Fräsen und Drehen von Schalen übernimmt die interne und externe Druckplattenstruktur (siehe Abbildung 3). Über die Gegendruckplatte können die Innen- und Außenprofile durch einmaliges Spannen, Drehen und Fräsen bearbeitet werden.
3. Auswahl der Werkzeuge für die Bearbeitung von Fräs-Dreh-Compounds
Das fünfachsige Fräs- und Drehbearbeitungszentrum DMG ist mit 40 ATC-Werkzeugmagazinen ausgestattet. Die Größe der Spindelkegelbohrung ist HSK-A100. Um der automatischen Werkzeugwechselfunktion des Bearbeitungszentrums vollen Spielraum zu geben, wird bei der Bearbeitung des Außengehäuses das Spannwerkzeug mit Iska-Modulbauweise verwendet (siehe Abbildung 4). In Verbindung mit der Drehfunktion des Spindelkopfes des DMG-Fünf-Koordinaten-Fräs- und Drehbearbeitungszentrums wird die Azimutlage des Drehwerkzeugs verändert. Mit einem Werkzeug werden verschiedene Positionen an der Innen- und Außenfläche bearbeitet, wodurch die Anzahl der Werkzeuge verringert und die Werkzeugkosten gesenkt werden.
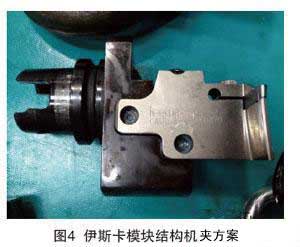
4. Programmierung von Fräsen Drehen Compoundbearbeitung
Entsprechend den Eigenschaften der CNC-Programmierung des Fräs- und Drehbearbeitungszentrums werden zwei Modi unterschieden: Fräsen und Bearbeiten. Der Fräsmodus ist DM_MILL und der Bearbeitungsmodus ist DM_TURN. Bei der Erstellung des 5-Achs-Kopplungsfräsprogramms müssen die 5-Achs-Werkzeugnasenverfolgung, die CNC-Bahnvorausschau G64 und die Koordinierungsfunktion für die Synchronisation der Bearbeitungsachsen FGROUP aktiviert werden. Zur Erstellung des CNC-Bearbeitungsprogramms wird die Auswuchtfunktion des Demag-Fünfachsen-Bearbeitungszentrums benötigt. Bei der auf dem Maschinensieb angezeigten Gegengewichtsposition werden die Gegengewichtsblöcke mit dem gleichen Gewicht entsprechend dem vom System vorgegebenen Gewicht zugeordnet, um das Gleichgewicht des Drehsystems zu gewährleisten.
Bei der Erstellung des Fräsprogramms wird die Nachbearbeitung der Fräsen-Drehen-Compound-Bearbeitung vom Siemens-Subsystem entwickelt. Anwendung von Siemens 840D Sprachanweisungen und maschinenspezifischen Merkmalen. Zum Beispiel TRAORI (1), CYCLE800, CYCLE81-CYCLE86, Polarkoordinaten. Die Werkzeugmaschine, Fräsen, Bohren, Bohren, Gewindebohren und andere Methoden sind in einer Maschine integriert. Die kombinierte Bearbeitungstechnologie Fräsen und Drehen realisiert die kombinierte Bearbeitung mehrerer Prozesse Drehen, Fräsen, Bohren und Bohren. Beim Drehen-Fräsen müssen die unebenen Teile des Aufmaßes unter der Bedingung entfernt werden, dass die Gesamtsteifigkeit ausreichend ist, damit das Aufmaß für Fräsen und Drehen gleich bleibt. Wählen Sie je nach Struktur und Steifigkeit des Teils das Fräsen, um die Wandstärke sicherzustellen, oder die Bearbeitung, um die Wandstärke sicherzustellen. Nachdem alle Abmessungen bearbeitet wurden, werden die technischen Bedingungen des Bezugspunkts gemessen und der Bezugspunkt repariert. Nachdem alle Dreh- und Fräsvorgänge abgeschlossen sind, wird gebohrt, gebohrt und gewindebohrt.
Für diesen Teil ist die Route zum Anordnen des NC-Prozesses wie folgt:
Grobes Fräsprofil (mit 0,3 mm Rand) - Innen- und Außenflächen grob drehen (mit 0,3 mm Rand) - Innen- und Außenflächen fein drehen (mit 0,1 mm Rand auf Bezugsebene) - Fertigfräsen- Präzisionsdrehdatum- Bohren und Bohren von radialen Löchern und Fräsen von Gewinden- Bohren und Bohren von Endflächen.
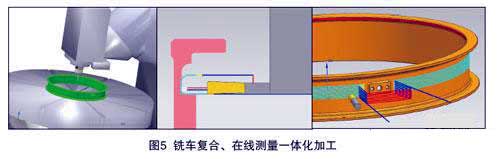
5. Online-Messung des Fräs- und Compoundierprozesses
Das fünfachsige Fräs- und Drehbearbeitungszentrum DMG ist mit Renishaw-Tastern und Infrarot-Empfängern mit Online-Messung ausgestattet. Bei der ultradünnen Shell-Car-Composite-Verarbeitung wird die Online-Messfunktion angewendet. Mit dem Renishaw-Messtaster zur Vervollständigung der automatischen Ausrichtung der Teile wird das Bearbeitungskoordinatensystem automatisch eingestellt und die integrierte Messung von Online-Messung und Fräsen durchgeführt (siehe Abb. 5). Das automatische Ausrichtungsverfahren für die Online-Messung von Gehäusen sieht wie folgt aus:
CYCLE800
TRAFOOF
DM_MILL
T999
M6 ...; ______ Einzelpunktmessung Z-Achse Nullposition, Koordinatenrahmen setzen G54 _______
_TUL = 1_TLL = -1
_PRNUM = 1_NMSP = 1_VMS = 0
_TSA = 20_FA = 15_KNUM = 1
_MVAR = 100_MA = 3
_SETVAL = 0
CYCLE978
G54; ____ Einzelpunktmessung Z-Achsen-Nullposition, Koordinatenrahmen setzen G54 _________ G0X0Y0Z-2; ____ Einzelpunktmessung X-, Y-Achsennullposition, Koordinatenrahmen G54 setzen _________ _TUL = 1_TLL = -1
_PRNUM = 1_NMSP = 1_VMS = 0
_TSA = 20_FA = 15_KNUM = 1
_MVAR = 101_MA = 3
_SETVAL = 433_STA1 = 0
_INCA = 90_CPA = 0_CPO = 0
_KNUM = 1
CYCLE979
G54; ____ Einzelpunktmessung X-, Y-Achsennullposition, Koordinatenrahmen G54 einstellen _________M28
G0Z500
M02
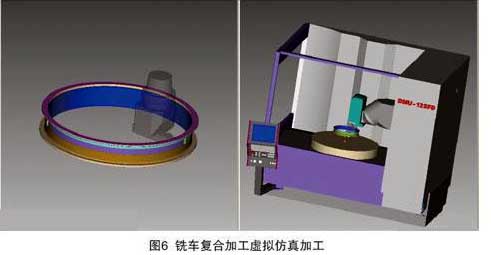
6. Simulation und Überprüfung des Fräs- und Walzcompound-Programms
VERICUT ist eine leistungsstarke Bearbeitungssimulationssoftware, die CNC-Programme durch Simulation analysiert. Es kann festgestellt werden, ob es Überschneidungen, Rest- und andere Phänomene in der Bearbeitung gibt, um Störungen und Kollisionen zu vermeiden und die Richtigkeit und Rationalität des NC-Bearbeitungsprogramms zu überprüfen. Insbesondere bei der Entwicklung neuer Teile kann die Richtigkeit des Programms durch eine Bearbeitungssimulation überprüft werden. Dies kann teure Teststückkosten einsparen, unnötige Bearbeitungszeit einsparen und eine sehr wichtige Rolle bei der Entwicklung neuer Teile spielen. Um die Genauigkeit des Fräsprogramms zu überprüfen, wurde die Simulationsumgebung des fünfachsigen Fräsbearbeitungszentrums DMU125FD mit der Software VERICUT7.0 erstellt. Die Überprüfung der virtuellen Simulationsverarbeitung des Ultradünnschalen-Autoverbund-Bearbeitungsprogramms ist abgeschlossen, wodurch die Richtigkeit des Programms sichergestellt wird. Die Struktur der Simulationswerkzeugmaschine ist in Abb. 6 dargestellt.
Durch vergleichende Analyse experimenteller Daten. Es wird nachgewiesen, dass die Technologie zum Fräsen und Drehen von Verbundwerkstoffen vorteilhaft ist, um die Bearbeitungseffizienz des Flugzeugtriebwerksgehäuses zu verbessern, die Vorrichtung zu schonen und die Bearbeitungskosten zu senken. Vermeiden Sie Korrekturfehler der Sekundärspannung durch Verformung des dünnwandigen Gehäuses und sichern Sie die Verarbeitungsqualität der dünnwandigen Maschine.
abschließend
Durch die Anwendung der kombinierten Fräs- und Drehbearbeitungstechnologie bei der Bearbeitung von dünnwandigen Luft- und Raumfahrtgehäusen wird die Bedeutung der Funktionen der komplexen Fräs- und Drehmaschinenausrüstung weiter erkannt. Beherrschte die automatische Ausrichtung, das Fräsen und das Zusammensetzen von Werkzeugwechseln, das Fräsen und die virtuelle Simulation von Fahrzeugverbundwerkstoffen sowie andere Bearbeitungstechnologien für die Online-Messung. Der typische Prozessverlauf der integrierten Bearbeitung der gesamten ringförmigen dünnwandigen Mantelfräsmaschine wird gebildet. Die kombinierte Bearbeitungstechnologie Fräsen und Drehen dient dazu, den Prozess zu verbessern und die Funktionen der Werkzeugmaschine voll auszuschöpfen. Die Prozessroute wurde verkürzt und Bearbeitungstechniken wie Online-Messung, Drehen und Fräsen sowie virtuelle Simulation wurden übernommen. Es stellt die Zuverlässigkeit des Verarbeitungsprozesses sicher, kann die Verarbeitungseffizienz erheblich verbessern, die Verarbeitungskosten senken und die Verarbeitungsqualität sicherstellen.
Die Auswahl der Fräs- und Dreh Composite-Verarbeitung Ausrüstung
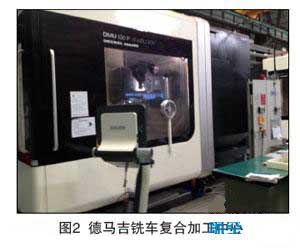
Die ultradünne Schalenbearbeitungsanlage wird aus dem 5-Koordinaten-Fräs- und Drehbearbeitungszentrum von Demag ausgewählt (siehe Abbildung 2). Die Maschine verwendet einen elektrischen Spindelkopf mit einem Winkel von 45 ° und wird von einem Linearmotor angetrieben. Das Servoantriebssystem zeichnet sich durch hohe Präzision, gute Zuverlässigkeit und schnelle Reaktion aus. Es gibt genügend statische und dynamische Steifigkeit, um sicherzustellen, dass das System eine gute dynamische Qualität und thermische Stabilität aufweist. Das Gerät sollte über eine hohe Präzision, hohe Zuverlässigkeit und eine Ethernet-Schnittstelle verfügen, um mit Computern und anderen Geräten zu vernetzen. Es realisiert die Übertragung von CNC-Bearbeitungsprogrammen, verschiedenen Prozessparametern und Maschinenzustandsinformationen und kann sich an die Bearbeitung schwer zerspanbarer Werkstoffe wie Hochtemperaturlegierungen und Titanlegierungen anpassen. Es kann Fräsen, Drehen, Bohren, Spreizen, Reiben, Bohren usw. in einer Aufspannung ausführen und kann zum präzisen Positionieren von Löchern in Luft- und Raumfahrtteilen sowie zum Vorschlichten und Schlichten von Außenflächen verwendet werden. Die Maschine ist kraftvoll gefräst und mit der Frässoftware SHOPMILL ausgestattet. Die Werkbank kann ein dynamisches Gleichgewicht herstellen und den Auswuchtpunkt analysieren, um die Drehfunktion zu unterstützen. Mit der Online-Erkennungsfunktion kann eine Online-Simulation von Auto und Fräsen realisiert werden. Die wichtigsten technischen Parameter der Maschine sind wie folgt:
Achsen-Verfahrweg: ≥1250mm;
Y-Achsen-Reisen: ≥1000mm;
Verfahrweg Z-Achse: ≥1000mm;
Werkbank größe: ≥ φ1250mm;
Maximaler Drehdurchmesser: ≥ φ1400mm;
Belastung der Werkbank: ≥2000 kg.
Drehbereich der C-Achse (Werkbank): ≥ ± 360 °, Positioniergenauigkeit: ≤ 7 ′ ′, Wiederholungspositioniergenauigkeit: ≤ 4 ′ ′.
Arbeitstisch fräsen maximale geschwindigkeit: ≥20r / min,
Maximale drehgeschwindigkeit: ≥500r / min,
Maximales Drehmoment (S1): ≥ 5400 N • m,
Maximale Leistung zum Wenden (S1): ≥35 kW.
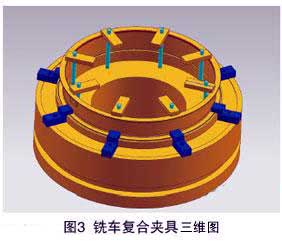
Die kombinierte Bearbeitungstechnologie Fräsen und Drehen muss die Bearbeitung der meisten Dimensionen in einer Aufspannung realisieren, und die Werkzeugaufnahme ist entscheidend für das Spiel. Andernfalls muss es viele Male gespannt werden, was die Verarbeitungseffizienz zwangsläufig verringert. Die Technologie des Fräsens und Drehens der Verbundbearbeitungstechnik besteht darin, dass die Innenfläche im Allgemeinen durch Drehen gedreht wird, die Außenfläche Drehen und Bohren und Fräsen umfasst und die Endfläche oder das radiale Loch durch Bohren, Bohren und Reiben bearbeitet wird. Daher muss für die kombinierte Bearbeitung von Fräsen und Drehen eine Vorrichtung entwickelt werden, die innen und außen positioniert und eingespannt werden kann und schnell zerlegt werden kann. Die ultradünne kombinierte Bearbeitungsvorrichtung zum Fräsen und Drehen von Schalen übernimmt die interne und externe Druckplattenstruktur (siehe Abbildung 3). Über die Gegendruckplatte können die Innen- und Außenprofile durch einmaliges Spannen, Drehen und Fräsen bearbeitet werden.
3. Auswahl der Werkzeuge für die Bearbeitung von Fräs-Dreh-Compounds
Das fünfachsige Fräs- und Drehbearbeitungszentrum DMG ist mit 40 ATC-Werkzeugmagazinen ausgestattet. Die Größe der Spindelkegelbohrung ist HSK-A100. Um der automatischen Werkzeugwechselfunktion des Bearbeitungszentrums vollen Spielraum zu geben, wird bei der Bearbeitung des Außengehäuses das Spannwerkzeug mit Iska-Modulbauweise verwendet (siehe Abbildung 4). In Verbindung mit der Drehfunktion des Spindelkopfes des DMG-Fünf-Koordinaten-Fräs- und Drehbearbeitungszentrums wird die Azimutlage des Drehwerkzeugs verändert. Mit einem Werkzeug werden verschiedene Positionen an der Innen- und Außenfläche bearbeitet, wodurch die Anzahl der Werkzeuge verringert und die Werkzeugkosten gesenkt werden.
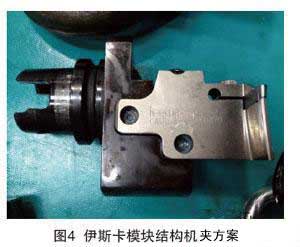
4. Programmierung von Fräsen Drehen Compoundbearbeitung
Entsprechend den Eigenschaften der CNC-Programmierung des Fräs- und Drehbearbeitungszentrums werden zwei Modi unterschieden: Fräsen und Bearbeiten. Der Fräsmodus ist DM_MILL und der Bearbeitungsmodus ist DM_TURN. Bei der Erstellung des 5-Achs-Kopplungsfräsprogramms müssen die 5-Achs-Werkzeugnasenverfolgung, die CNC-Bahnvorausschau G64 und die Koordinierungsfunktion für die Synchronisation der Bearbeitungsachsen FGROUP aktiviert werden. Zur Erstellung des CNC-Bearbeitungsprogramms wird die Auswuchtfunktion des Demag-Fünfachsen-Bearbeitungszentrums benötigt. Bei der auf dem Maschinensieb angezeigten Gegengewichtsposition werden die Gegengewichtsblöcke mit dem gleichen Gewicht entsprechend dem vom System vorgegebenen Gewicht zugeordnet, um das Gleichgewicht des Drehsystems zu gewährleisten.
Bei der Erstellung des Fräsprogramms wird die Nachbearbeitung der Fräsen-Drehen-Compound-Bearbeitung vom Siemens-Subsystem entwickelt. Anwendung von Siemens 840D Sprachanweisungen und maschinenspezifischen Merkmalen. Zum Beispiel TRAORI (1), CYCLE800, CYCLE81-CYCLE86, Polarkoordinaten. Die Werkzeugmaschine, Fräsen, Bohren, Bohren, Gewindebohren und andere Methoden sind in einer Maschine integriert. Die kombinierte Bearbeitungstechnologie Fräsen und Drehen realisiert die kombinierte Bearbeitung mehrerer Prozesse Drehen, Fräsen, Bohren und Bohren. Beim Drehen-Fräsen müssen die unebenen Teile des Aufmaßes unter der Bedingung entfernt werden, dass die Gesamtsteifigkeit ausreichend ist, damit das Aufmaß für Fräsen und Drehen gleich bleibt. Wählen Sie je nach Struktur und Steifigkeit des Teils das Fräsen, um die Wandstärke sicherzustellen, oder die Bearbeitung, um die Wandstärke sicherzustellen. Nachdem alle Abmessungen bearbeitet wurden, werden die technischen Bedingungen des Bezugspunkts gemessen und der Bezugspunkt repariert. Nachdem alle Dreh- und Fräsvorgänge abgeschlossen sind, wird gebohrt, gebohrt und gewindebohrt.
Für diesen Teil ist die Route zum Anordnen des NC-Prozesses wie folgt:
Grobes Fräsprofil (mit 0,3 mm Rand) - Innen- und Außenflächen grob drehen (mit 0,3 mm Rand) - Innen- und Außenflächen fein drehen (mit 0,1 mm Rand auf Bezugsebene) - Fertigfräsen- Präzisionsdrehdatum- Bohren und Bohren von radialen Löchern und Fräsen von Gewinden- Bohren und Bohren von Endflächen.
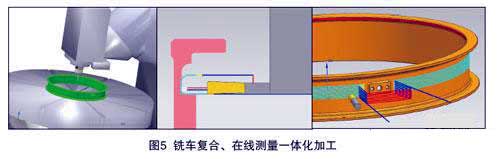
5. Online-Messung des Fräs- und Compoundierprozesses
Das fünfachsige Fräs- und Drehbearbeitungszentrum DMG ist mit Renishaw-Tastern und Infrarot-Empfängern mit Online-Messung ausgestattet. Bei der ultradünnen Shell-Car-Composite-Verarbeitung wird die Online-Messfunktion angewendet. Mit dem Renishaw-Messtaster zur Vervollständigung der automatischen Ausrichtung der Teile wird das Bearbeitungskoordinatensystem automatisch eingestellt und die integrierte Messung von Online-Messung und Fräsen durchgeführt (siehe Abb. 5). Das automatische Ausrichtungsverfahren für die Online-Messung von Gehäusen sieht wie folgt aus:
CYCLE800
TRAFOOF
DM_MILL
T999
M6 ...; ______ Einzelpunktmessung Z-Achse Nullposition, Koordinatenrahmen setzen G54 _______
_TUL = 1_TLL = -1
_PRNUM = 1_NMSP = 1_VMS = 0
_TSA = 20_FA = 15_KNUM = 1
_MVAR = 100_MA = 3
_SETVAL = 0
CYCLE978
G54; ____ Einzelpunktmessung Z-Achsen-Nullposition, Koordinatenrahmen setzen G54 _________ G0X0Y0Z-2; ____ Einzelpunktmessung X-, Y-Achsennullposition, Koordinatenrahmen G54 setzen _________ _TUL = 1_TLL = -1
_PRNUM = 1_NMSP = 1_VMS = 0
_TSA = 20_FA = 15_KNUM = 1
_MVAR = 101_MA = 3
_SETVAL = 433_STA1 = 0
_INCA = 90_CPA = 0_CPO = 0
_KNUM = 1
CYCLE979
G54; ____ Einzelpunktmessung X-, Y-Achsennullposition, Koordinatenrahmen G54 einstellen _________M28
G0Z500
M02
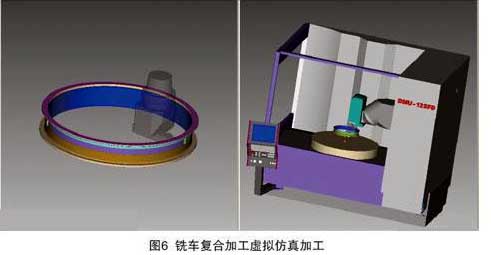
6. Simulation und Überprüfung des Fräs- und Walzcompound-Programms
VERICUT ist eine leistungsstarke Bearbeitungssimulationssoftware, die CNC-Programme durch Simulation analysiert. Es kann festgestellt werden, ob es Überschneidungen, Rest- und andere Phänomene in der Bearbeitung gibt, um Störungen und Kollisionen zu vermeiden und die Richtigkeit und Rationalität des NC-Bearbeitungsprogramms zu überprüfen. Insbesondere bei der Entwicklung neuer Teile kann die Richtigkeit des Programms durch eine Bearbeitungssimulation überprüft werden. Dies kann teure Teststückkosten einsparen, unnötige Bearbeitungszeit einsparen und eine sehr wichtige Rolle bei der Entwicklung neuer Teile spielen. Um die Genauigkeit des Fräsprogramms zu überprüfen, wurde die Simulationsumgebung des fünfachsigen Fräsbearbeitungszentrums DMU125FD mit der Software VERICUT7.0 erstellt. Die Überprüfung der virtuellen Simulationsverarbeitung des Ultradünnschalen-Autoverbund-Bearbeitungsprogramms ist abgeschlossen, wodurch die Richtigkeit des Programms sichergestellt wird. Die Struktur der Simulationswerkzeugmaschine ist in Abb. 6 dargestellt.
Ergebnisanalyse
Probleme in Routineverfahren und Routen vorhanden:
(1) Der Prozess des Drehens, Fräsens, Bohrens und Bohrens ist zu verstreut, die Wartezeit für die Produktionsvorbereitung und der Umsatz zwischen den Prozessen ist lang und es werden mehr Verarbeitungsgeräte benötigt, was die Verarbeitungseffizienz und den Lieferplan beeinflusst.
(2) Die tatsächlichen Werte einiger Dimensionen liegen nahe an den theoretischen Grenzwerten. Wenn nicht kontrolliert, können die Teilabmessungen außerhalb der Toleranz liegen.
(3) Das NC-Programm und die Bearbeitungsparameter müssen optimiert und verfeinert werden.
(4) Der Werkzeugverbrauch ist zu groß.
Durch die Bearbeitung von Prüflingen und Realteilen vor Ort nach dem Lean-Engineering-Konzept. Die Vorteile der neuen Technologie und Methoden werden anhand der Anzahl der Prozesse, des Verarbeitungszyklus, des Qualitätsstatus und der Verarbeitungskosten analysiert. Die Datenanalyse und der Vergleich sind in Tabelle 1 gezeigt.
Probleme in Routineverfahren und Routen vorhanden:
(1) Der Prozess des Drehens, Fräsens, Bohrens und Bohrens ist zu verstreut, die Wartezeit für die Produktionsvorbereitung und der Umsatz zwischen den Prozessen ist lang und es werden mehr Verarbeitungsgeräte benötigt, was die Verarbeitungseffizienz und den Lieferplan beeinflusst.
(2) Die tatsächlichen Werte einiger Dimensionen liegen nahe an den theoretischen Grenzwerten. Wenn nicht kontrolliert, können die Teilabmessungen außerhalb der Toleranz liegen.
(3) Das NC-Programm und die Bearbeitungsparameter müssen optimiert und verfeinert werden.
(4) Der Werkzeugverbrauch ist zu groß.
Durch die Bearbeitung von Prüflingen und Realteilen vor Ort nach dem Lean-Engineering-Konzept. Die Vorteile der neuen Technologie und Methoden werden anhand der Anzahl der Prozesse, des Verarbeitungszyklus, des Qualitätsstatus und der Verarbeitungskosten analysiert. Die Datenanalyse und der Vergleich sind in Tabelle 1 gezeigt.
Durch vergleichende Analyse experimenteller Daten. Es wird nachgewiesen, dass die Technologie zum Fräsen und Drehen von Verbundwerkstoffen vorteilhaft ist, um die Bearbeitungseffizienz des Flugzeugtriebwerksgehäuses zu verbessern, die Vorrichtung zu schonen und die Bearbeitungskosten zu senken. Vermeiden Sie Korrekturfehler der Sekundärspannung durch Verformung des dünnwandigen Gehäuses und sichern Sie die Verarbeitungsqualität der dünnwandigen Maschine.
abschließend
Durch die Anwendung der kombinierten Fräs- und Drehbearbeitungstechnologie bei der Bearbeitung von dünnwandigen Luft- und Raumfahrtgehäusen wird die Bedeutung der Funktionen der komplexen Fräs- und Drehmaschinenausrüstung weiter erkannt. Beherrschte die automatische Ausrichtung, das Fräsen und das Zusammensetzen von Werkzeugwechseln, das Fräsen und die virtuelle Simulation von Fahrzeugverbundwerkstoffen sowie andere Bearbeitungstechnologien für die Online-Messung. Der typische Prozessverlauf der integrierten Bearbeitung der gesamten ringförmigen dünnwandigen Mantelfräsmaschine wird gebildet. Die kombinierte Bearbeitungstechnologie Fräsen und Drehen dient dazu, den Prozess zu verbessern und die Funktionen der Werkzeugmaschine voll auszuschöpfen. Die Prozessroute wurde verkürzt und Bearbeitungstechniken wie Online-Messung, Drehen und Fräsen sowie virtuelle Simulation wurden übernommen. Es stellt die Zuverlässigkeit des Verarbeitungsprozesses sicher, kann die Verarbeitungseffizienz erheblich verbessern, die Verarbeitungskosten senken und die Verarbeitungsqualität sicherstellen.
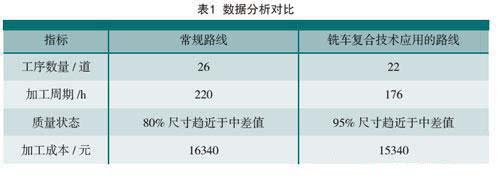